
Archives
Contribute
|
Technology - Rapid Solidification Using Containerless Processing
|
|
David J. Fair and Rakesh Venkatesh 09/17/2005
Every metal object we see around us has specific material properties
such as yield strength, fracture toughness, and electrical
resistivity. Many of these properties are dependent on the
crystalline structure of the metal on a microscopic level. For
example two pieces of identical alloy composition may have vastly
different yield strengths because one of them may have very large
crystal grains, while the other may have very fine crystal
grains. One of them may have been heat-treated or work hardened
leading to substantially better strength or hardness. Thus the
manufacturing processes with which a metal is created is very important
to the life and usefulness of that metal. Among other
things, the Thermal Analysis of Materials Processing Laboratory (TAMPL)
at Tufts University studies a particular facet of the creation of
metals, solidification. Using both an electromagnetic levitator
(EML) and an electrostatic levitator (ESL), we are studying the process
of rapid solidification. Rapid solidification occurs
when a liquid is brought to a temperature below its freezing point
while still a liquid. In this state, the metal is called
“undercooled†or “supercooledâ€. Because this state is very
unstable thermodynamically (the metal really wants to be a solid, not a
liquid), as soon as one tiny piece of solid is formed inside the
liquid, the entire piece of metal solidifies very quickly. This
tiny piece of solid is called a nucleus, and its formation is called
nucleation. A nucleus can form by liquid atoms sticking to either
some surface on its container, or some impurity in the liquid; this is
called heterogeneous nucleation – a nucleation that occurs on something
that is not part of the alloy itself. A nucleus can also form by
liquid atoms sticking to each other, or homogeneous nucleation.
Because it is much easier for heterogeneous nucleation to occur than
homogeneous, we must minimize the possibility of heterogeneous
nucleation in order to reach the undercooled state in our tests.
The biggest place for atoms to stick in a molten metal is the walls of
the container in which it is sitting, so this should be the first thing
we remove. In order to remove the container from the process, we
melt and solidify our samples in either the EML or the ESL, which allow
us to simply suspend the sample in an either a magnetic or electric
field, not touching anything.
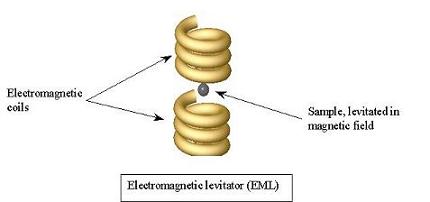

We
also use only high purity metals to create our alloys to minimize the
amount of impurities inside the sample. In the lab, we frequently
have undercoolings as great as 150° C. At such undercoolings, the
solid crystals grow through the undercooled liquid at speeds of 3-10
meters per second. Because our samples are small (EML samples are
~7mm, ESL samples are ~2mm), the entire sample solidifies in less than
a millisecond. The only way to view these events is using a very
high-speed camera, 40,000 to 100,000 frames per second.
There are certain kinds of alloys which exhibit a phenomenon known as
“double recalescence†when they are undercooled below a certain
Temperature. Because solidification occurs so rapidly in these
scenarios, the energy of the liquid that is lost to the creation of
atomic bonds (latent heat of fusion) is suddenly released into the
sample and the surrounding environment. The result is a sudden
rise in temperature that is visible to the eye as a flash of
light. This is called a recalescence. A double recalescence
is caused by a second phase transformation, from one type of solid to
another type of solid. This means that these alloys actually
solidify twice! First they transform from the liquid phase to a
metastable solid phase, then after a short incubation time, they
transform to a different solid phase, this time a stable solid
phase. The result of this whole process is that the finished
material has a uniform, very small crystal grain structure, which means
that it has favorable material properties. The temperature plot
below shows a typical double recalescence event. The sample heats
up (1), the sample melts (2), the sample undercools (3), the first
recalescence (4), the second recalescence (5), and the sample cools as
a solid (6).
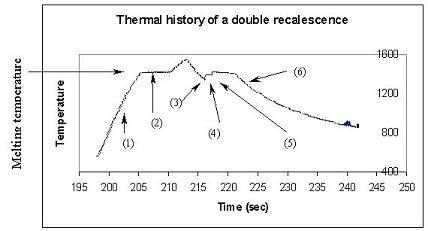 Unfortunately,
there are many factors involved in this event. Because the growth
velocities of the two phase transformations are different functions of
undercooling, there are regimes where the first is faster than the
second and vice-versa. Therefore, in order to have the entire
material experience the double recalescence and to have the favorable
microstructure, a third factor comes into play, the incubation time of
the metastable phase. We know that the incubation time
of the metastable phase, commonly referred to as the delay time, is a
strong function of at least the alloy composition and
undercooling. Past research has shown that it is also a function
of something else, and that is the focus of our current research.
When comparing delay time data taken in the EML with that
taken in the ESL, it is clear that there is roughly an order of
magnitude difference between them. 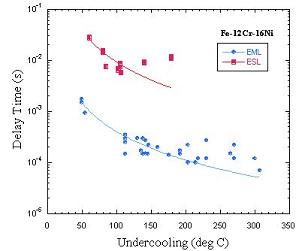
We have considered 3 possible factors so far, based on the differences
in test environments: first, the effect of alloy change due to
preferential evaporation of Chromium from the melt, second, the effect
of difference of sample size between EML and ESL samples, and third,
the presence of magneto-hydrodynamic (MHD) convection in EML and its
absence in ESL. While we have shown that the first two cannot be
the driving factors in the difference in delay times, it is possible
and appears likely that the MHD convection may be an important
factor. This research is sponsored by NASA grants
NAG8-1685, NNM04AA31G, and the NASA GSRP grant NAGT5-50445. The
ESL facility is located at the NASA Marshall Spaceflight Center in
Huntsville, Alabama; the EML facility is located at Tufts
University.
(Rakesh Venkatesh and David Fair are Ph.D candidates in the Mechanical Engineering at Tufts University. Rakesh can be reached at rakesh.venkatesh@tufts.edu. )
|
You may also access this article through our web-site http://www.lokvani.com/
|
Rakesh Venkatesh
David J. Fair
|